Coarse vs Fine Threads
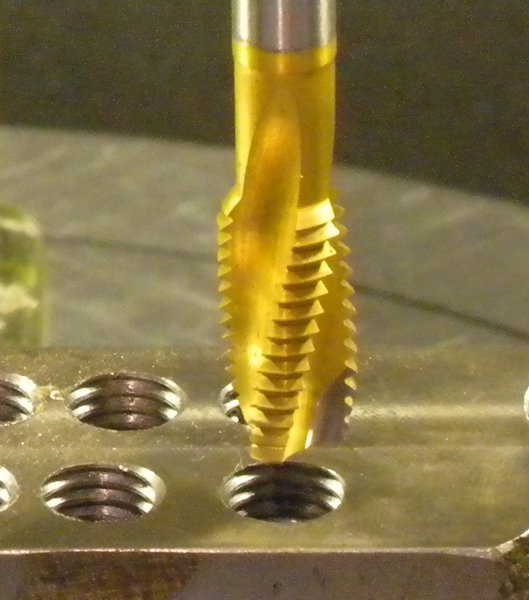
Thread is a key factor that affects how fastener parts (such as nuts, bolts, and screws) hold the workpiece and the machine together, work closely during the service life, and maintain their integrity for a long time. Two types of threaded thick taps and fine taps are mainly used in work, and these two types have their own advantages and appropriate uses
The main difference between coarse and fine threads is the root area of the nominal bolt area. Fine thread geometries with more threads per inch inherently have a shallower thread depth, resulting in a larger small diameter and a larger root area.
Coarse Threads
For most applications, course threads have the following advantages:
Easier and faster assembly, provide a better start, and reduce the chance of cross-threading.
Scratches and burrs from handling are unlikely to affect the assembly.
They are unlikely to get stuck in temperature applications and joints that will form corrosion.
When screwed into low-strength metal, it is not easy to peel off.
Easier to knock in fragile materials and/or fragile materials.
Fine Threads
For applications with specific strength or other requirements, fine threads may be a quality fastener.
Due to its larger cross-sectional area, its strength is about 10% of that of a coarse thread.
In very hard materials, thin threads are easier to tap.
Because the helix angle is smaller, it can be adjusted more accurately.
In the case of limited engagement length, they provide greater strength.
Since the thread cross-section is small, a thinner wall thickness can be used.
UNC - Unified Coarse Threads
Major Diameter | Threads per inch | Major Diameter | Tap Drill Size | Pitch | |
(in) | (tpi) | (in) | (mm) | (mm) | (mm) |
#1 - 64 | 64 | 0.073 | 1.854 | 1.5 | 0.397 |
#2 - 56 | 56 | 0.086 | 2.184 | 1.8 | 0.453 |
#3 - 48 | 48 | 0.099 | 2.515 | 2.1 | 0.529 |
#4 - 40 | 40 | 0.112 | 2.845 | 2.35 | 0.635 |
#5 - 40 | 40 | 0.125 | 3.175 | 2.65 | 0.635 |
#6 - 32 | 32 | 0.138 | 3.505 | 2.85 | 0.794 |
#8 - 32 | 32 | 0.164 | 4.166 | 3.5 | 0.794 |
#10 - 24 | 24 | 0.19 | 4.826 | 4 | 1.058 |
#12 - 24 | 24 | 0.216 | 5.486 | 4.65 | 1.058 |
1/4" - 20 | 20 | 0.25 | 6.35 | 5.35 | 1.27 |
5/16" - 18 | 18 | 0.313 | 7.938 | 6.8 | 1.411 |
3/8" - 16 | 16 | 0.375 | 9.525 | 8.25 | 1.587 |
7/16" - 14 | 14 | 0.438 | 11.112 | 9.65 | 1.814 |
1/2" - 13 | 13 | 0.5 | 12.7 | 11.15 | 1.954 |
9/16" - 12 | 12 | 0.563 | 14.288 | 12.6 | 2.117 |
5/8" - 11 | 11 | 0.625 | 15.875 | 14.05 | 2.309 |
3/4" - 10 | 10 | 0.75 | 19.05 | 17 | 2.54 |
7/8" - 9 | 9 | 0.875 | 22.225 | 20 | 2.822 |
1" - 8 | 8 | 1 | 25.4 | 22.85 | 3.175 |
1 1/8" - 7 | 7 | 1.125 | 28.575 | 25.65 | 3.628 |
1 1/4" - 7 | 7 | 1.25 | 31.75 | 28.85 | 3.628 |
1 3/8" - 6 | 6 | 1.375 | 34.925 | 31.55 | 4.233 |
1 1/2" - 6 | 6 | 1.5 | 38.1 | 34.7 | 4.233 |
1 3/4" - 5 | 5 | 1.75 | 44.45 | 40.4 | 5.08 |
2" - 4 1/2 | 4 1/2 | 2 | 50.8 | 46.3 | 5.644 |
2 1/4" - 4 1/2 | 4 1/2 | 2.25 | 57.15 | 52.65 | 5.644 |
2 1/2" - 4 | 4 | 2.5 | 63.5 | 58.5 | 6.35 |
2 3/4" - 4 | 4 | 2.75 | 69.85 | 64.75 | 6.35 |
3" - 4 | 4 | 3 | 76.2 | 71.1 | 6.35 |
3 1/4" - 4 | 4 | 3.25 | 82.55 | 77.45 | 6.35 |
3 1/2" - 4 | 4 | 3.5 | 88.9 | 83.8 | 6.35 |
3 3/4" - 4 | 4 | 3.75 | 95.25 | 90.15 | 6.35 |
4" - 4 | 4 | 4 | 101.6 | 96.5 | 6.35 |
UNF - Unified National Fine Threads
Major Diameter | Threads per inch | Major Diameter | Tap Drill Size | Pitch | |
(in) | (tpi) | (in) | (mm) | (mm) | (mm) |
#0 - 80 | 80 | 0.06 | 1.524 | 1.25 | 0.317 |
#1 - 72 | 72 | 0.073 | 1.854 | 1.55 | 0.353 |
#2 - 64 | 64 | 0.086 | 2.184 | 1.9 | 0.397 |
#3 - 56 | 56 | 0.099 | 2.515 | 2.15 | 0.453 |
#4 - 48 | 48 | 0.112 | 2.845 | 2.4 | 0.529 |
#5 - 44 | 44 | 0.125 | 3.175 | 2.7 | 0.577 |
#6 - 40 | 40 | 0.138 | 3.505 | 2.95 | 0.635 |
#8 - 36 | 36 | 0.164 | 4.166 | 3.5 | 0.705 |
#10 - 32 | 32 | 0.19 | 4.826 | 4.1 | 0.794 |
#12 - 28 | 28 | 0.216 | 5.486 | 4.7 | 0.907 |
1/4" - 28 | 28 | 0.25 | 6.35 | 5.5 | 0.907 |
5/16" - 24 | 24 | 0.313 | 7.938 | 6.9 | 1.058 |
3/8" - 24 | 24 | 0.375 | 9.525 | 8.5 | 1.058 |
7/16" - 20 | 20 | 0.438 | 11.112 | 9.9 | 1.27 |
1/2" - 20 | 20 | 0.5 | 12.7 | 11.5 | 1.27 |
9/16" - 18 | 18 | 0.563 | 14.288 | 12.9 | 1.411 |
5/8" - 18 | 18 | 0.625 | 15.875 | 14.5 | 1.411 |
3/4" - 16 | 16 | 0.75 | 19.05 | 17.5 | 1.587 |
7/8" - 14 | 14 | 0.875 | 22.225 | 20.4 | 1.814 |
1" - 12 | 12 | 1 | 25.4 | 23.25 | 2.117 |
1 1/8" - 12 | 12 | 1.125 | 28.575 | 26.5 | 2.117 |
1 1/4" - 12 | 12 | 1.25 | 31.75 | 29.5 | 2.117 |
1 3/8" - 12 | 12 | 1.375 | 34.925 | 32.75 | 2.117 |
1 1/2" - 12 | 12 | 1.5 | 38.1 | 36 | 2.117 |
Which is stronger: fine or coarse threads taps?
Which one offers better corrosion resistance: fine thread or coarse thread?
In practical applications, the thread profile of a fastener has nothing to do with its corrosion resistance. This is usually determined by the plating or coating on the fastener. For an in-depth guide, please refer to our white paper on corrosion resistance.
When to use fine-threaded fasteners and coarse-threaded fasteners ?
1. Fine threaded fasteners should be used in conjunction with thick gauge metal applications. Threaded fasteners should be used in conjunction with thin metal applications. To
2. Fine threaded fasteners should be used in combination with thicker and stronger metal applications. Layer threaded fasteners should be used in combination with more brittle materials (such as plywood, OSB, and 2" x 4" wood).
In our electric tapping machine system,when you choose the tapping size,
that Coarse Threads will automatic generated, and if you need fine thread, you can adjust in the system via touch screen.

CONTACT US
Tell us your raw material and project budget to get quotations within 24 hours.
WhatsApp Us: +86 159 27 555 863
Want the best price & newest metalworking machinery buying guide,tips and trends sent straightly to your box?Sign up for Armpro’s monthly newsletter,we’re free for your consultation and Offer you the most suitable solutions!
The Buyer's Guide
- Tapping Machine: The Ultimate Buying Guide in 2021
- Electric Tapping Machines:the Ultimate Buying Guide in 2021
- Drilling Machine: The Ultimate Buying Guide in 2021
- Grinding Machine:The Ultimate Buying Guide in 2021
- Metal Band Saw Machine :The Complete Buying Guide in 2021
- Pneumatic Tapping Machine:The Complete Importing Guide in 2021
- Bench Tapping Machine:The Complete Buying Guide in 2021
- CNC Tapping Machine:The Complete Buying Guide In 2021
- Magnetic Base Drill Machine:The Ultimate Buying Guide in 2021
- Drilling And Tapping Machine:The Complete Buying Guide in 2021
Tell us your material or budget,we'll reply you ASAP within 24 hours.